About
We are your partner for future-oriented solutions!
Whitecell Eisenhuth is a company that has been in existence since 1945 and currently employs 70 people.
The company focuses on component manufacturing for fuel cells and electrolysers. It is also an established supplier to the automotive, healthcare and mechanical engineering industries with core competencies in mould making and small and medium series of moulded parts made of plastic, rubber and silicone.
Whitecell Eisenhuth has been actively working on the development of bipolar plates for fuel cells based on plastic/graphite composites since 2006. Whitecell Eisenhuth technologies are already being used successfully in fuel cells and electrolysers. We have been awarded numerous prizes in recent years for our high level of innovation and successful developments. Innovation drives us as a team. Convince yourself.
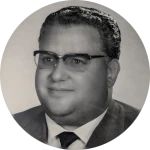
Founding
as Wilhelm Eisenhuth & Sohn Herbert.
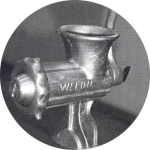
Meat grinder production
The founders Wilhelm and Herbert Eisenhuth buy up aircraft wrecks and melt them down into aluminium. This is used to produce cast parts, including the much-produced “WELOH” die-cast meat grinder.
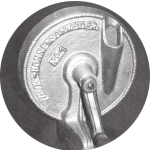
Household appliances
Construction of household appliances, such as bean-shredding machines and meat grinders.
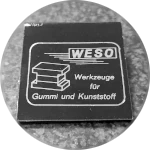
Mould making begins
Start of the production of rubber and silicone tools.
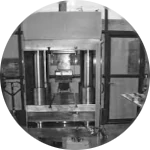
Rubber press
Construction of a first press for vulcanising rubber parts.
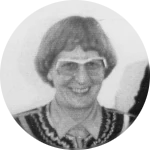
Managing director takes over
The co-founder Herbert Eisenhuth dies, shortly afterwards also Wilhelm Eisenhuth. Afterwards, Elisabeth Eisenhuth (later Hickmann) – one of the few women in business life at the time – takes over the company’s fortunes and successfully manages it for many years.
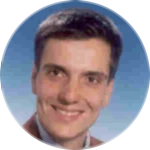
Family business
Son Dr. Thorsten Hickmann joins the company.
New Managing Director
Dr. Thorsten Hickmann takes over all shares in the company.
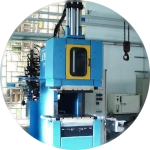
Rubber press
A first injection moulding press for sampling rubber parts is purchased. Initially only for sampling tools, later also for the company’s own production.
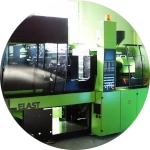
Injection moulding machine
The first of many injection moulding machines is purchased. Initially only for sampling tools, later also for the company’s own production.
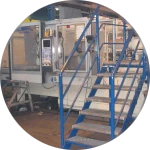
Hydrogen
Entry into the hydrogen sector. Production line for the manufacture of bipolar plates goes into operation.
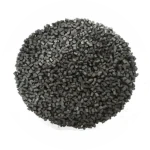
Compound
An in-house twin-screw extruder is purchased to produce compounds for bipolar plates.
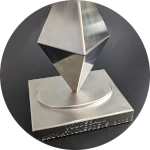
Volksbank Innovationspreis 2012
A process was created with which the seal for an MEA can be applied directly to the bipolar plate.
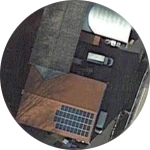
PV-Anlage
The first string of an own PV system is put into operation to generate green electricity itself.
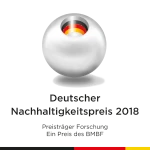
Deutscher Nachhaltigkeitspreis – Forschung
For the development of a bio fuel cell with which electricity can be generated from waste water.
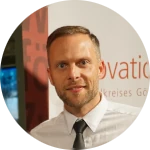
New Managing Director
Toni Adamek becomes managing director.
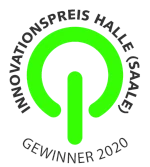
Innovationspreis Halle (Saale)
For our titanium composite plates with the help of which the material costs for electrolysers can be reduced by up to 50%.
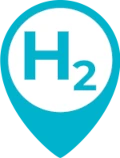
Mission Hydrogen
We focus on solutions for fuel cells, electrolysers and redox flow batteries.
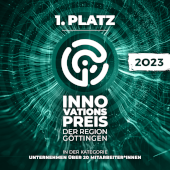
Innovationspreis der Region Göttingen 2023
Winner in the category of companies with more than 20 employees. The innovation consists of the production of gaphite bipolar plates for fuel cells by injection moulding.
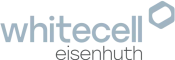
Whitecell Eisenhuth
Takeover by Whitecell Power AG and start of the partnership with the Whitecell Group.
Our Services
Whitecell Eisenhuth in Numbers
350
Active tools in series production
120
Hydrogen projects per year
12
Innovation awards
22
Patents
Our motivation: Progress – Quality – Safety – Flexibility
Progress
We are driven by research and innovation and regularly benchmark ourselves against other companies.
The success is impressive: We have won a total of twelve innovation awards so far.
We are especially proud of the German Sustainability Award in the research category 2018, which we received together with the TU Clausthal, the TU Braunschweig and the KIT.
Quality & Safety
Quality has a high priority for us. We have been ISO 9001 certified since 1997.
All products are tested in our quality laboratory to ensure our proven standards.
We continuously adapt our quality system to meet the latest requirements.
Data security also enjoys a high priority, we have been TISAX certified since 2015.
Flexibility
We are able to adapt quickly to new requirements, due to our flat hierarchies.
Our teams are interested in gaining new experiences and mastering new challenges.
We are constantly improving and optimising our own processes.